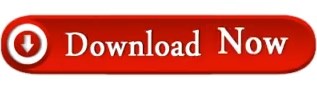

The direct entrainment of a low velocity suction fluid by a motive fluid results in an unavoidable loss of kinetic energy owing to impact and turbulence originally possessed by the motive fluid. Since ejectors approach a theoretically isentropic process, overall efficiency is expressed as a function of entrainment efficiency. This ratio is of little value in the selection and design of ejectors. Typically, efficiency involves a comparison of energy output to energy input. The diagram below right shows the thermal changes on a Mollier diagram for a typical ejector using high pressure steam as the motivating fluid and saturated vapor as the suction fluid.Įjector Efficiency: There are many accepted formulae to express ejector efficiency. The pressure and velocity changes are also shown graphically for the process directly below the ejector diagram. Both Ma and Mb are then recompressed through the diffuser to 5. The suction fluid Mb enters at 3, mixes with the motivating fluid in the mixing chamber 4. The diagram below left illustrates a typical ejector.Ī high pressure motivating fluid Ma and Mb enters at 1, expands through the converging-diverging nozzle to 2.
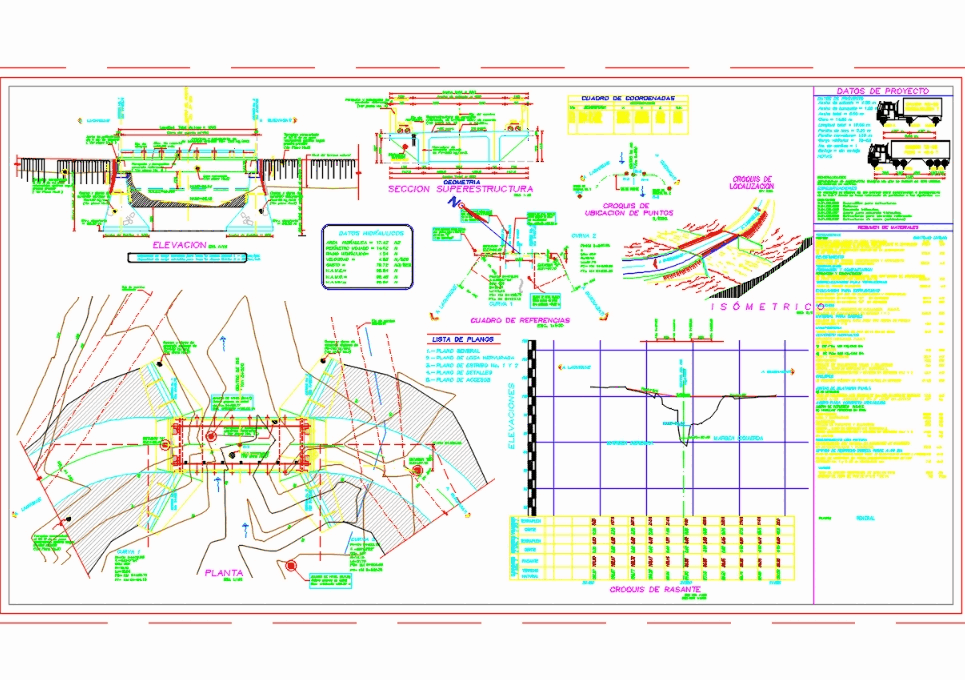
Basic Construction: Ejectors are composed of three basic parts: a nozzle, a mixing chamber and a diffuser. Since the pressure between the first two stages of four-stage ejector or, the first three stages of a five-stage ejector is too low to permit condensing, these stages are designed as non-condensing with the subsequent stages condensing. For extremely low suction pressures, 4, 5 and 6-stage ejectors are utilized see diagram below. This permits the recycle of ejector steam to the boiler. Where surface type after-condensers are used, the condesate for the main condenser can be pumped through the inter-condenser and after-condenser as cooling water. Three-stage non-condensing units use relatively large quantities of motivating steam and are not generally recommended.Įjector systems often incorporate the use of an after-condenser to condense the atmospheric stage motive steam. When condensable loads are small or nonexistent, only one intercondenser following the second stage is typically used. This design is generally recommended for suction pressures from 4. An inter-condenser of either the surface or direct-contact type is used between the stages to condense steam from the preceding stage and reduce load. Multi-stage condensing ejectors are available in two or more stages. These designs are frequently used where a low first cost is more important than operating economy, for intermittent use or for applications where water is not available. Steam consumption in these units is relatively high as each successive stage is required to handle the load and motive steam of the stage ahead of it.
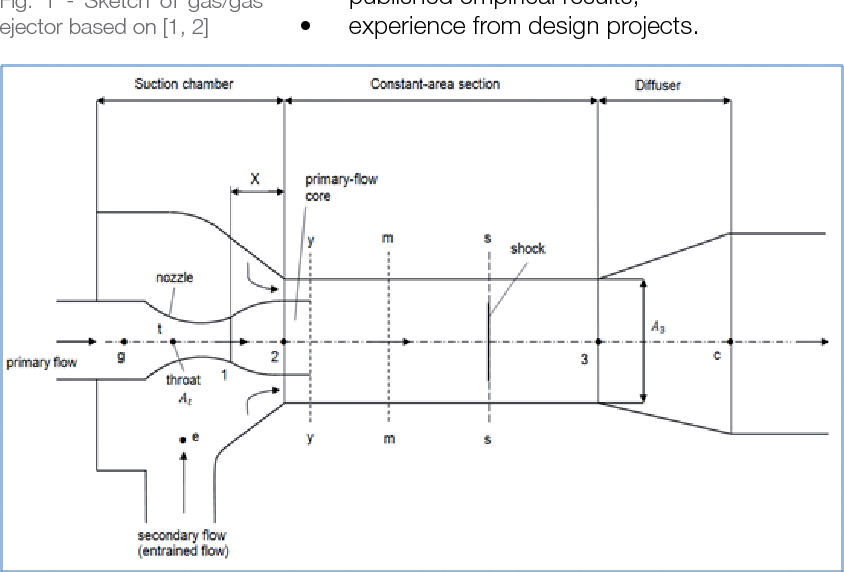
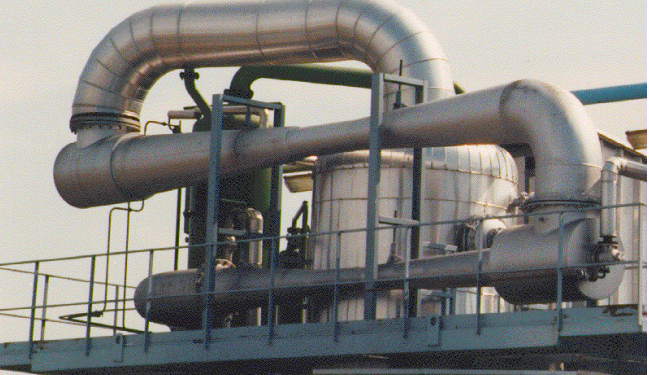
Multi-stage non-condensing ejectors shown right are used where lower suction pressures are specified. Single-stage units typically discharge at or near atmospheric pressure. They are generally recommended for pressure from atmospheric to 3 Hg. Single-stage ejectors shown right are the simplest and most commonly used design. Ejectors are generally categorized into one of four basic types: single-stage, multi-stage non-condensing, multi-stage condensing and multi-stage with both condensing and non-condensing stages. This change from pressure head to velocity head is the basis of the jet vacuum principle. This is based on the theory that a properly designed nozzle followed by a properly designed throat or venturi will economically make use of high pressure fluid to compress from a low pressure region to a higher pressure. Steam ejectors are designed to convert the pressure energy of a motivating fluid to velocity energy to entrain suction fluid and then to recompress the mixed fluids by converting velocity energy back into pressure energy.
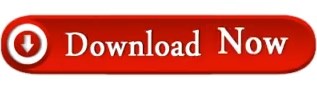